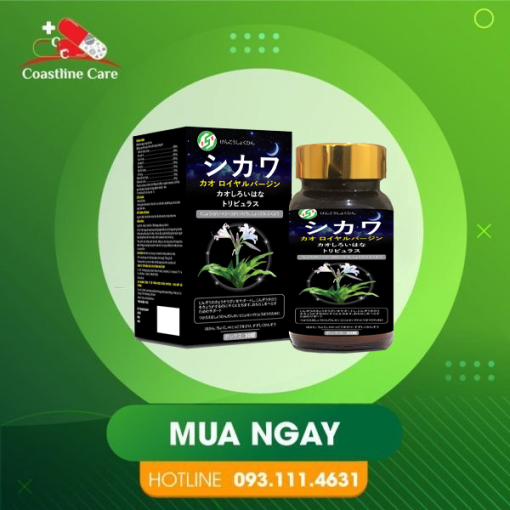
This kind of tracking record can be utilized to communicate the staff’s progress to management and customers. New insights may very well be received because the investigation progresses. For example, any person checking the length of a component may have observed hurt. This harm could then be entered into an current Ishikawa diagram then transferred to the tracking record.
Excellent circles typically encompass a little group of employees within the same perform place who fulfill on a regular basis to recognize, assess, and remedy do the job-connected complications. The process involves:
Explicar temas en distintos niveles educativos. Se pueden explicar hechos históricos y procesos naturales y sociales cuando es necesario hacer referencia a múltiples causas.
Just investigating the lights could choose time and resources faraway from the investigation so the first step could be to view if a component is mounted.
The customer’s description doesn't should be correct. It need to replicate the customer’s terms and be distinct that it is a quote rather than an observation. For example, a difficulty assertion might start as “Customer X reports Solution A won't function.
Criar um diagrama do zero é fileácil com uma ferramenta para criar diagrama de Ishikawa on the internet. Para começar a preencher um diagrama existente, o modelo de diagrama de ossos de peixe é um recurso útil para visualizar as causas potenciais de um problema.
An mistake nha thuoc tay happened when saving your issue. Be sure to report it to the website administrator. Added information:
Ishikawa diagrams are more practical when There's a acknowledged challenge that a business can determine. The corporate need to also be able to observe the condition, as this info will finally be fed to the diagram.
La SAS est de fait devenu l’un des statuts juridiques les plus prisés des créateurs de PME et des groupes de sociétés souhaitant créer nha thuoc tay des filiales.
They might be biased or incomplete if team users usually do not actively take part in the analysis procedure.
The 6Ms from the Ishikawa diagram are essential aspects used to detect and examine issues inside of a process. These aspects include:
Paso five: Realizamos el mismo proceso con las demás causas o espinas mayores. El aspecto del gráfico terminado es el siguiente:
In this instance, using five Whys led towards the genuine explanation for the failure – nha thuoc tay the light bulbs burned out. Had the 5 Whys not been applied, then the worker could are retrained, but exactly the same staff or someone else can have created a similar or a different blunder due to weak lighting.
Every lead to or reason for imperfection is actually a supply of variation. Causes are generally grouped into important categories to recognize and classify these sources of variation.